Probability of failure is a concept used to prepare capital replacement or reserve fund studies for facility managers and condominium corporations, as well as to plan maintenance and replacement schedules for equipment in large facilities. Probability of failure compensates for the fact that visual inspections are often imperfect, in that the critical components may not be visible. Even if the critical component is visible, predicting accurately when
failure will occur is often difficult.
The concept of probability of failure is pretty simple:
The probability of failure of any mechanical component or mechanical system increases as the component ages. Even a brand new component can fail; it’s just not very likely. For example, of the 1,000 computers that are sold by a computer manufacturer every day, one or two will have a major failure within the first day or two of use. The odds are this will not happen, but in the extreme minority of cases it does.
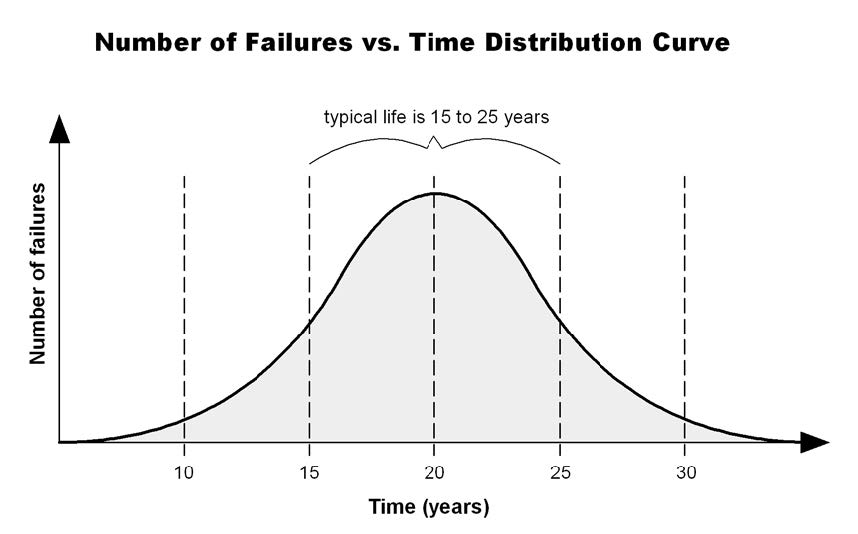
Figure 1 illustrates a typical distribution of failures of a specific number of mechanical components, over a period of time. From this graph, we can make several observations:
- The likelihood of a failure in the first few years is very low. However, some failures will occur!
- The typical life of this component is 20 years. This means that the greatest number of component failures occurs in year 20. However, in terms of overall number of failures, the typical life span is better represented by 15 to 25 years.
After year 25, the number of failures drops dramatically. This because there are very few components from the initial group left in service. This also illustrates that while some components may last 30 years or more, these are as exceptional as components that lasted only 10 years
Assigning a probability of failure to a system involves:
- Identifying the critical component of the system (like the heat exchanger in a heating system or the compressor in an air conditioning system)
- Identifying the age of the critical component. We can identify the age of the entire unit readily from the serial number. We can do the same for a compressor in an air conditioning system. However, it is more difficult to know if and when a heat exchanger was replaced.
- Determining the expected life (from personal experience, historic and/or statistical experience)
- Assigning a probability of failure in general terms (low, medium, or high)
- Adjusting the probability of failure if necessary, based on the site conditions
Take, for example, a hot water boiler with a copper heat exchanger. Statistically, this component may
have a life expectancy of 20 years. The following table is an example of how we could categorize the probability of failure, based on different conditions:
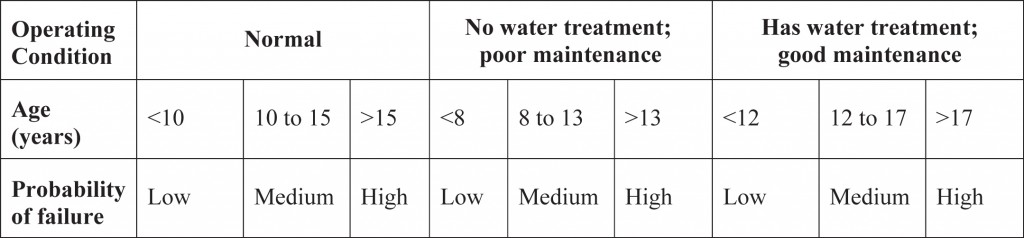
While it is important to understand how mechanical systems work and to be able to identify common deficiencies, the most important part of the mechanical system inspection is identifying the ages of the main systems or components and assigning a probability of failure for your client. Describing all the minor repairs necessary to the 25 year old boiler is not as important as identifying the likelihood for boiler replacement in the short term and of course the associated replacement cost.